We Love Kimono Project 8
Fuse-nori 伏糊: Covering with paste
Once the Itome-oki 糸目置 is complete, the craftsman moves on to the process called fuse-nori 伏糊.

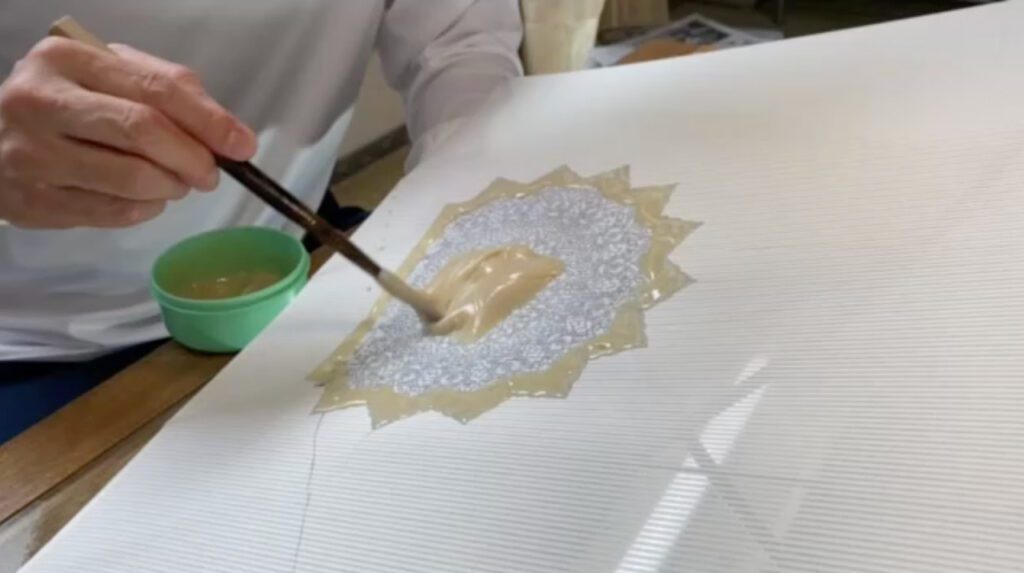
Fuse-nori is a mixture of sticky rice, rice bran, salt, and water. Its texture is thick like a paste. The craftsman applies the fuse-nori evenly to cover the whole area where the Itome-oki, the paste-dyeing, is done.
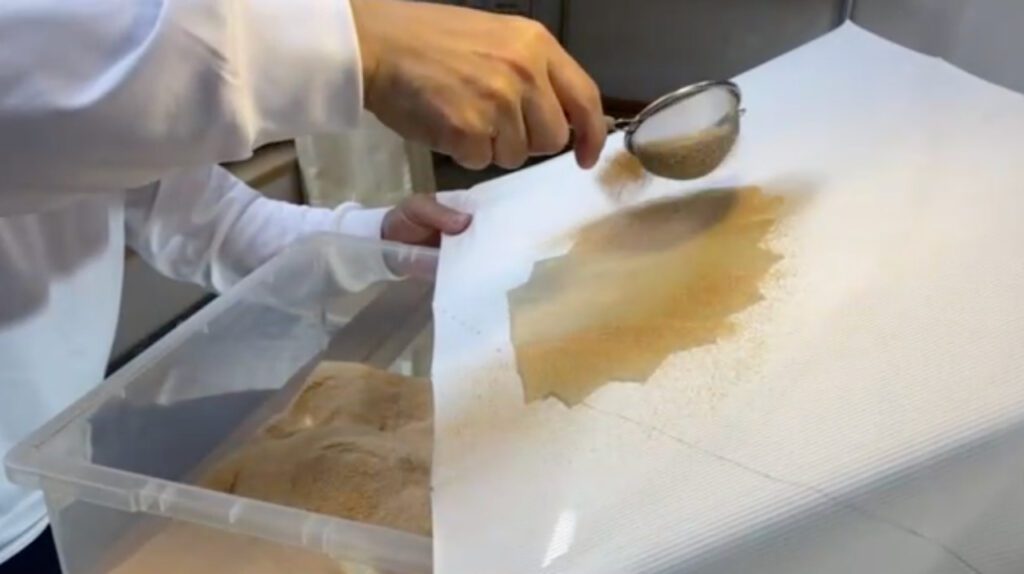
S/he then sprinkles sawdust on the fuse-nori. The covered area with fuse-nori and the sawdust is left intact when the rest of the fabric is dyed with the basic color.
Jizome地染: Dyeing the basic color
The next step is to dye the fabric with the base color. This is called 地染jizome.
The standard length of a kimono fabric is about 12 – 13 meters, or forty feet. The craftsman first clamps both ends of the fabric and hangs it across. A very long room is needed for this process.
S/he places bamboo sticks in an arch shape across the short side of the fabric, so that the tension of the sticks keeps the fabric straight. About two hundred sticks are used. Once the fabric is hung long with its surface stretched flat, it’s ready to spread the dye.

Using a flat brush, the craftsman swiftly spreads the dye so that the color is spread evenly all through the fabric. Mamiya-san’s design has this river-like flow. The craftsman implements a special technique called bokashi暈し to shade off the wisteria color at the border.
Both spreading the dye evenly across the long fabric and shading off the color naturally require a high level of skills, acquired only with experience.
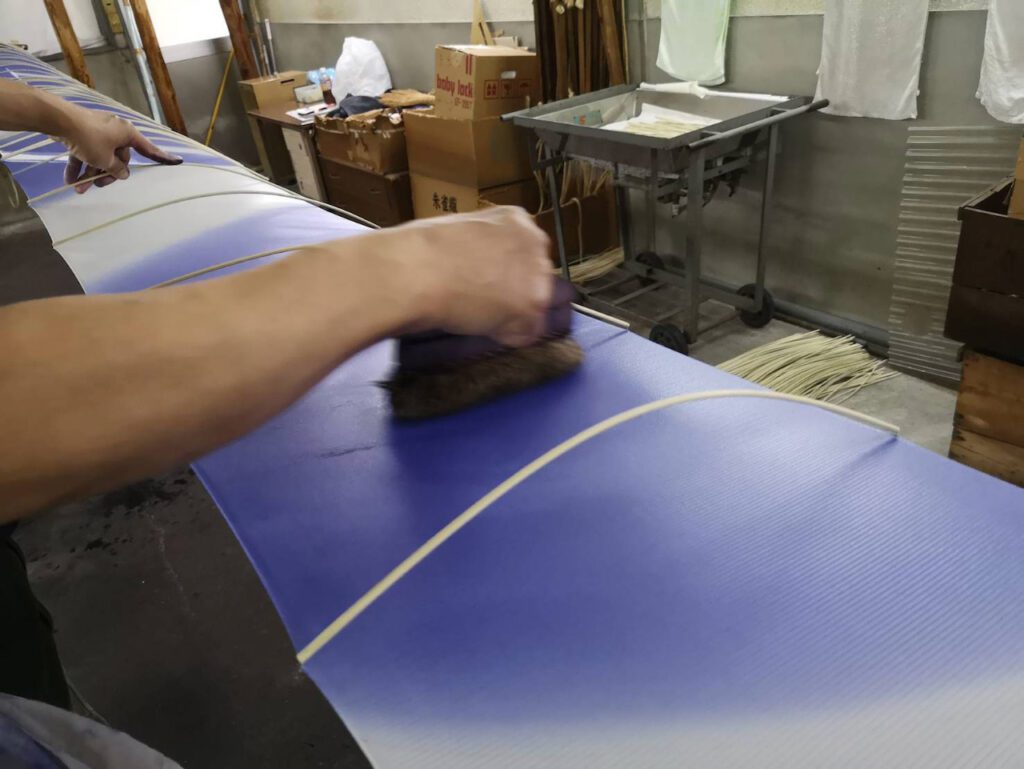
The craftsman spreads the dye on both the front and the back side of the fabric. On the back side, you can see the bamboo sticks spreading the fabric with the tension.

Mushi 蒸し:Steaming
Once the basic color is applied, the fabric is left to dry. Then the fabric is folded loosely and put into a small enclosure where it is steamed at a high temperature for twenty to fifty minutes. The darker the color, the longer it takes to steam. This way the color of the dye seeps into the yarns of the fabric thoroughly.
Mizumoto 水元 : Rinsing off with water
Once the fabric is steamed, it’s time to wash away the excessive dye and fuse-nori.
In the old days, one would see kimono craftspeople washing their kimono in the Kamo River and other rivers around Kyoto.
Contamination of the river water, however, became a major concern. In 1971 washing out the kimono fabric on the river water was completely banned. Yuzen makers had to create an alternative method.
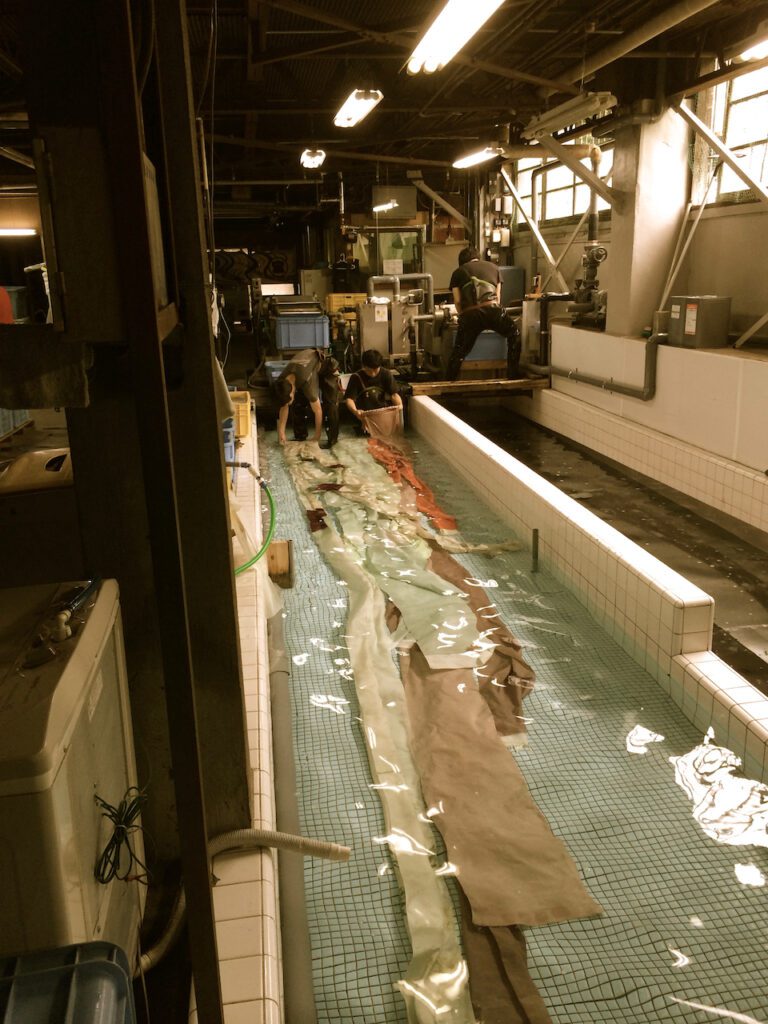
The photo above shows how the washing-out process is carried out today. Kyoto has abundant underground water. Now the water is pumped through the well into an indoor pool. The water used to wash the kimono fabric is treated before it flows back into the wastewater system.